HDPE Pipe Solutions for Engineers
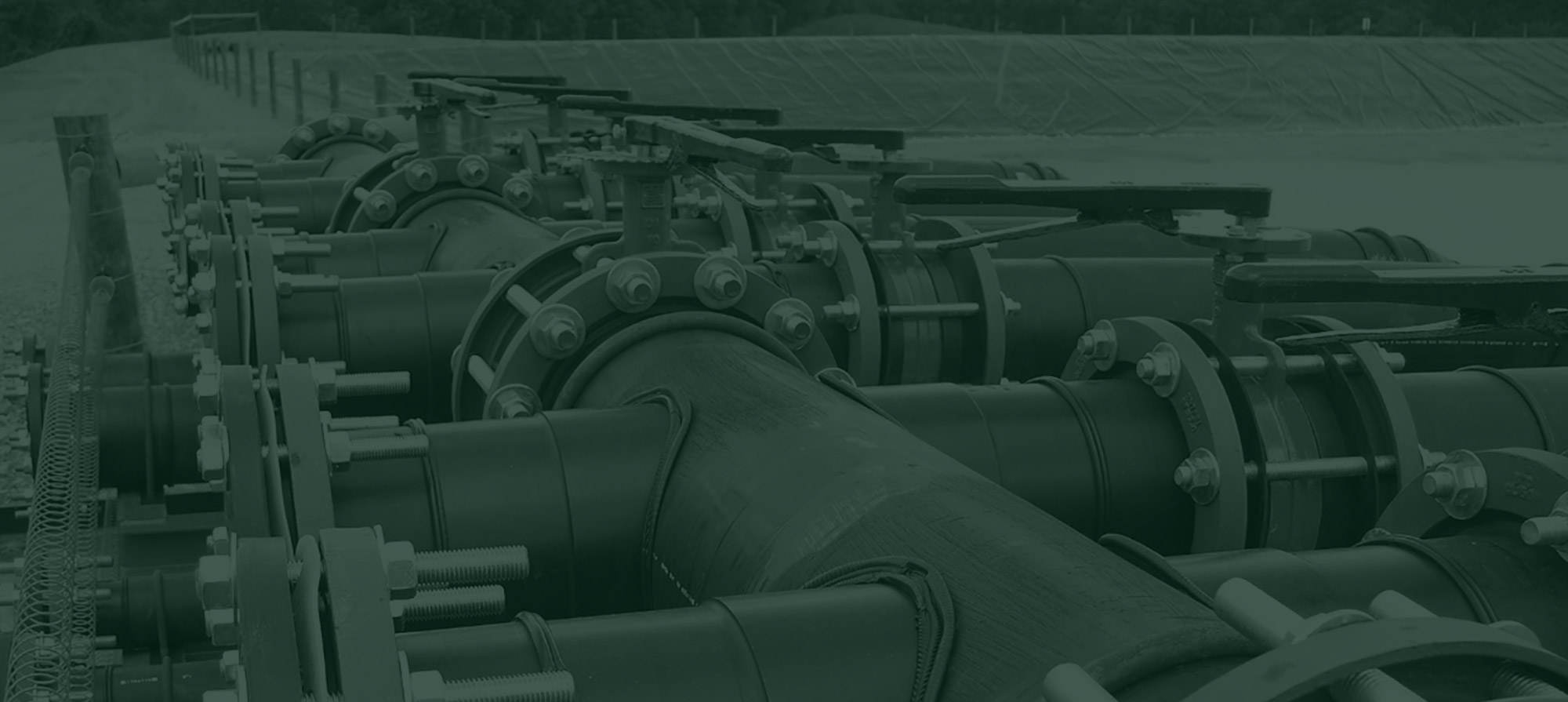
Lee Supply: Leading the Way to a Greener Infrastructure with HDPE Pipe Solutions
Sustainability
The decision-making process for piping systems involves various factors, with sustainability playing a crucial role. Lee Supply, a leader in the industry, emphasizes the use of High-Density Polyethylene (HDPE) pipes for their inherent ductility, durability, and eco-friendly characteristics.
Transportation
HDPE pipes offer a significant advantage in transportation, with a high strength-to-weight ratio. Compared to traditional materials like iron or concrete, HDPE pipes are lighter, requiring fewer truckloads for delivery. This not only reduces energy consumption but also contributes to a more efficient and sustainable transportation process.
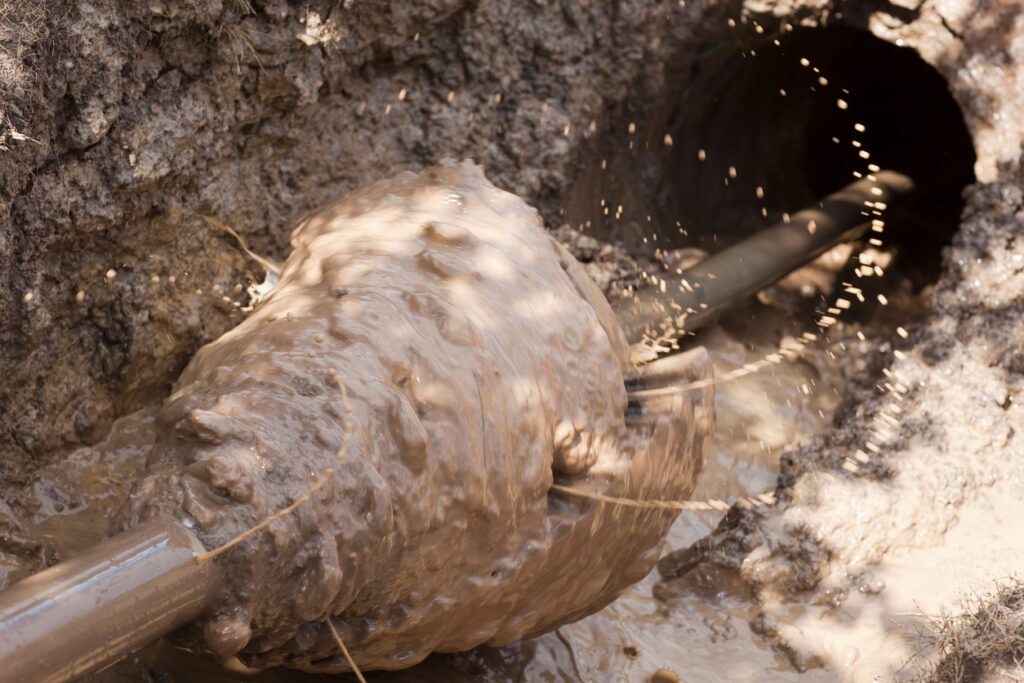
Installation
The lightweight and flexible nature of HDPE pipes result in lower installation costs and a reduced carbon footprint. Lee Supply promotes trenchless installation techniques, such as horizontal directional drilling, further minimizing environmental impact and enhancing overall sustainability.
Carbon Footprint
HDPE pipes boast a considerably lower carbon footprint compared to traditional piping materials. Lee Supply actively participates in initiatives to reduce reliance on fossil fuels in the production and transportation of HDPE pipes, contributing to a more environmentally friendly approach.
Service Life
With superior chemical and corrosion resistance, HDPE pipe from Lee Supply offer a service life exceeding 100 years. Studies confirm lower failure rates, reduced leakage, and lower maintenance, ensuring a reliable and long-lasting infrastructure.
Joining
Lee Supply focuses on robust joining technologies for HDPE pipes, minimizing system leakage and optimizing overall performance. Thermal fusion technologies ensure leak-free joints, saving precious natural resources and reducing the carbon footprint associated with water treatment and distribution.
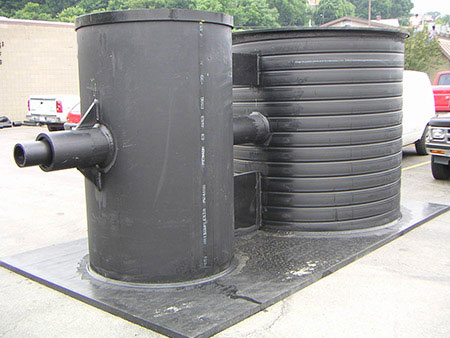
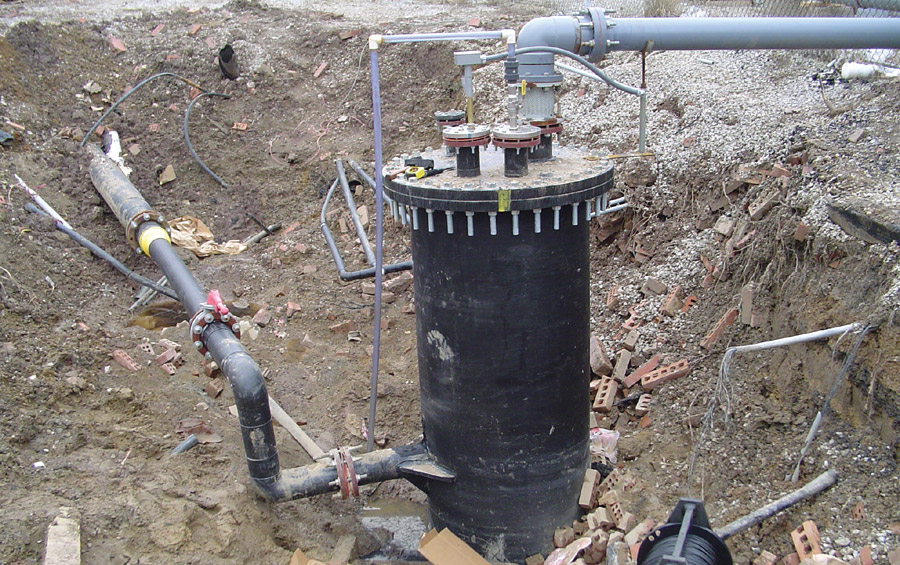
Life Cycle Cost
HDPE pipes prove to be a cost-effective alternative when considering life cycle costs. Lee Supply emphasizes the economic benefits of HDPE pipes, taking into account factors like chemical resistance, ease of installation, and strong, leak-free joints.
Recyclability – Circular Economy
Lee Supply actively explores recycling technologies for HDPE pipes, contributing to a circular economy. Initiatives like utilizing recycled PE in the production process demonstrate a commitment to sustainability, reducing waste and promoting responsible repurposing of materials.
Plastic Pipe – A Commitment to Sustainability
Lee Supply’s dedication to sustainability is evident throughout its operations. By embracing HDPE pipes and advancing recycling efforts, the company ensures a “green” infrastructure solution, meeting present needs without compromising the ability of future generations to meet their own.
Why Engineers Should Consider HDPE from Lee Supply
1. Unmatched Durability
Join the ranks of municipalities prioritizing water conservation by choosing HDPE pipe from Lee Supply. HDPE offers a leak-free system, providing a fused monolithic system that ensures reliability. Its flexibility and toughness make it suitable for various applications, including trenchless installations.
2. Longevity and Low Lifecycle Costs
Engineers can rely on HDPE pipe systems for longevity, exceeding 100 years without typical failure issues. With zero pitting, cracking, or corrosion, HDPE ensures a durable and reliable solution. Furthermore, HDPE boasts one of the lowest lifecycle costs among municipal pipe materials, making it an economically sound choice.
3. Trenchless and Cost-Effective Installation
HDPE’s heat fusion methods, such as butt fusion and electrofusion, create leak-proof joints stronger than the pipe itself. This method significantly reduces the number of fittings or clamps needed, making it a cost-effective choice. The flexibility of HDPE also allows for efficient installations, especially in trenchless projects.
4. Resistance to Flow Reduction
HDPE’s smooth surface resists scale build-up, ensuring constant flow rates throughout its lifespan. Unlike other piping materials, HDPE maintains its flow capacity over time, minimizing the need for adjustments and ensuring efficient water distribution.
5. Environmental Responsibility
Sustainability and efficiency are at the forefront of infrastructure considerations. HDPE pipe contribute to a greener future by being corrosion-resistant, reducing leaks, and lasting up to a century. Its fusion methods and low excavation requirements also align with environmentally conscious engineering practices.